Guide
Christian Cavallo
Condividi:
Uno dei processi industriali più antichi e ancora più fondamentali noti all’uomo è la fusione dei metalli. Iniziato nell’antichità per creare gioielli e armi, la fusione è un processo in cui il metallo liquido viene versato all’interno di alcuni stampi per produrre rapidamente forme complesse. Nei tempi moderni, sono state sviluppate procedure standard per creare parti altamente complesse, in particolare con un processo noto come microfusione. La fusione di investimento utilizza cera, liquami e stampi per produrre parti a bassa tolleranza e ad alta risoluzione senza il fastidio di metodi più tradizionali. Il processo di microfusione, come funziona, i suoi vantaggi e le sue applicazioni saranno mostrati in questo articolo in modo che i progettisti possano potenzialmente implementare questa tecnica nei propri progetti.
Che cos’è la microfusione e come funziona?
La fusione di investimento è un tipo di processo di fusione mediante il quale è possibile realizzare rapidamente parti altamente complesse (per saperne di più sulla fusione, leggi il nostro articolo sui tipi di processi di fusione). Ci sono quattro fasi principali per i processi di microfusione, mostrato in Figura 1, e spiegato di seguito.
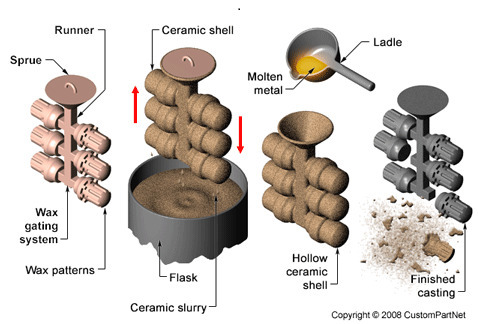
Figura 1: Processo di microfusione, passo dopo passo
Credito immagine: https://www.custompartnet.com/wu/investment-casting
Il primo passo consiste nella creazione del modello di cera che alla fine sarà la forma finale della parte(s). Cera è utilizzato perché è facilmente fuso e riutilizzato, ma questo significa anche che un modello di cera può essere utilizzato solo una volta ogni volta che una parte è fatta. Questa limitazione richiede al produttore di avere una sorta di stampo master, che può essere riutilizzato per creare i modelli di cera. Questi possono essere costosi perché devono essere adattati a ciascuna parte e sono difficili da perfezionare se sono necessarie tolleranze particolarmente basse. Tuttavia, se molti di questi stampi sono realizzati, possono essere collegati tramite una barra di cera (nota come “runner”) che consente di versare molte parti. Infine, una tazza di versamento in ceramica (nota come “sprue”) viene aggiunta alla parte superiore del modello di cera, in modo che i produttori abbiano un imbuto per versare il metallo fuso nello stampo finale.
La seconda fase del processo di microfusione è quando questo modello di cera finalizzato, completo di guide e canali, viene immerso in un impasto refrattario ceramico. Questo liquido di solito contiene silice estremamente fine, acqua e altri leganti. Una volta immerso, la parte sarà coperta in un sottile strato di slurry, che è effettivamente uno stampo del modello di cera. Questa fase di immersione viene eseguita molte volte per ottenere un certo spessore del rivestimento (spesso 5-10mm), quindi la parte viene asciugata. Dopo l’essiccazione, la parte viene capovolta e riscaldata per rimuovere l’umidità in eccesso e sciogliere la cera all’interno. Ora, i produttori sono lasciati con uno stampo ceramico cavo della loro parte desiderata.
Il terzo passaggio avverrà subito dopo il secondo, dove i produttori verseranno il metallo fuso nello stampo ceramico quando è ancora caldo dal processo di essiccazione/fusione. Questo preriscaldamento dal passaggio precedente impedisce al metallo fuso di danneggiare lo stampo ceramico, oltre a migliorare il flusso del metallo in angoli fini/aree di dettaglio. Inoltre, mentre l’assemblaggio si raffredda, sia lo stampo in ceramica che il metallo si restringono, fornendo una migliore precisione dimensionale al modello di cera originale. Dopo che il metallo è stato fuso, i produttori aspettano che si raffreddi completamente.
Il quarto e ultimo passo per la fusione di investimento è quello di rompere lo stampo ceramico quando è completamente solido. Questo viene spesso fatto con getti d’acqua o altri metodi per rimuovere lo strato ceramico senza danneggiare il metallo sottostante. A questo punto, le parti finite sono pronte per essere tagliate dalle loro guide e pulite fino alla finitura del prodotto finale desiderato.
Vantaggi e svantaggi della microfusione
La microfusione è un metodo di fusione molto popolare e per una buona ragione. Ha molti vantaggi rispetto ad altri metodi e fornisce parti altamente dettagliate fedeli ai loro stampi; tuttavia, ci sono alcuni notevoli svantaggi che devono essere discussi.
Di seguito sono riportati i principali vantaggi del processo di microfusione:
- Consente la fusione di parti estremamente complesse e estremamente accurate con una buona finitura superficiale, direttamente dallo stampo
- Può essere lanciato molto sottile (~0.015 in) sezioni con tolleranze incredibilmente basse (~0,003 in)
- Consente l’uso di quasi tutti i metalli in grado di fondere (alluminio, bronzo, ferro, ecc.)
- Il processo di microfusione può essere automatizzato, generando rapidamente un’enorme quantità di parti
- La cera può essere recuperata e riutilizzata per molti modelli
Questi vantaggi hanno un prezzo significativo, quindi esaminiamo gli svantaggi della microfusione:
- Parti sono meglio comportati in piccole dimensioni, del peso fino a 75 kg, con grandi parti di essere generalmente più adatto per altri processi di fusione
- Il processo è complesso e coinvolge tipicamente costose attrezzature e/o tecnici per operare
- L’alto costo degli stampi per fare i modelli di cera limiti di processi di produzione ad alto volume progetti
- Parti con core o fori più piccoli 1.6 mm o fori più profondi di 1.5 volte il diametro della parte sono difficili da investimento cast
Così, mentre altamente preciso e facilmente riproducibile, microfusione ha un costo elevato e lavorazioni complesse. Inoltre, ci sono alcune geometrie delle parti che non possono essere realizzate con questo tipo di fusione, quindi controlla le proprietà della tua parte per vedere se è compatibile.
Applicazioni della microfusione
La microfusione è un ottimo processo se si desiderano dettagli, riproducibilità e grandi volumi di prodotto. Mentre generalmente più costoso di altri processi di fusione come la colata in sabbia, è di gran lunga il metodo più semplice e veloce per fabbricare piccole forme apparentemente impossibili (scopri di più sulla colata in sabbia nel nostro articolo tutto sulla colata in sabbia). Può, quindi, essere utilizzato in qualsiasi numero di applicazioni, ma è particolarmente utile nei settori aerospaziale e automobilistico, in quanto questi mercati hanno bisogno di grandi volumi di parti complesse che devono essere esatte. Anche le applicazioni di generazione di energia, petrolio e gas e armi da fuoco beneficiano notevolmente della microfusione, poiché richiedono anche parti piccole ma accurate.
La quantità di applicazioni è effettivamente illimitata, quindi l’uso della microfusione aumenterà solo nel tempo. I produttori dovrebbero considerare la microfusione un processo se la precisione dimensionale e il volume delle parti sono specifiche importanti. Se queste non sono esigenze di guida per il progetto, o se sono necessarie parti di grandi dimensioni, il prezzo elevato e la complessità della microfusione potrebbero non pagare. Indipendentemente da ciò, il processo di microfusione è un’invenzione antica ma versatile che migliorerà la produttività e l’affidabilità nella maggior parte dei processi di produzione in cui è implementato.
Sommario
Questo articolo ha presentato una breve panoramica del processo di microfusione. Per informazioni su altri prodotti, consulta le nostre guide aggiuntive o visita la piattaforma Thomas Supplier Discovery per individuare potenziali fonti di approvvigionamento o visualizzare i dettagli su prodotti specifici.