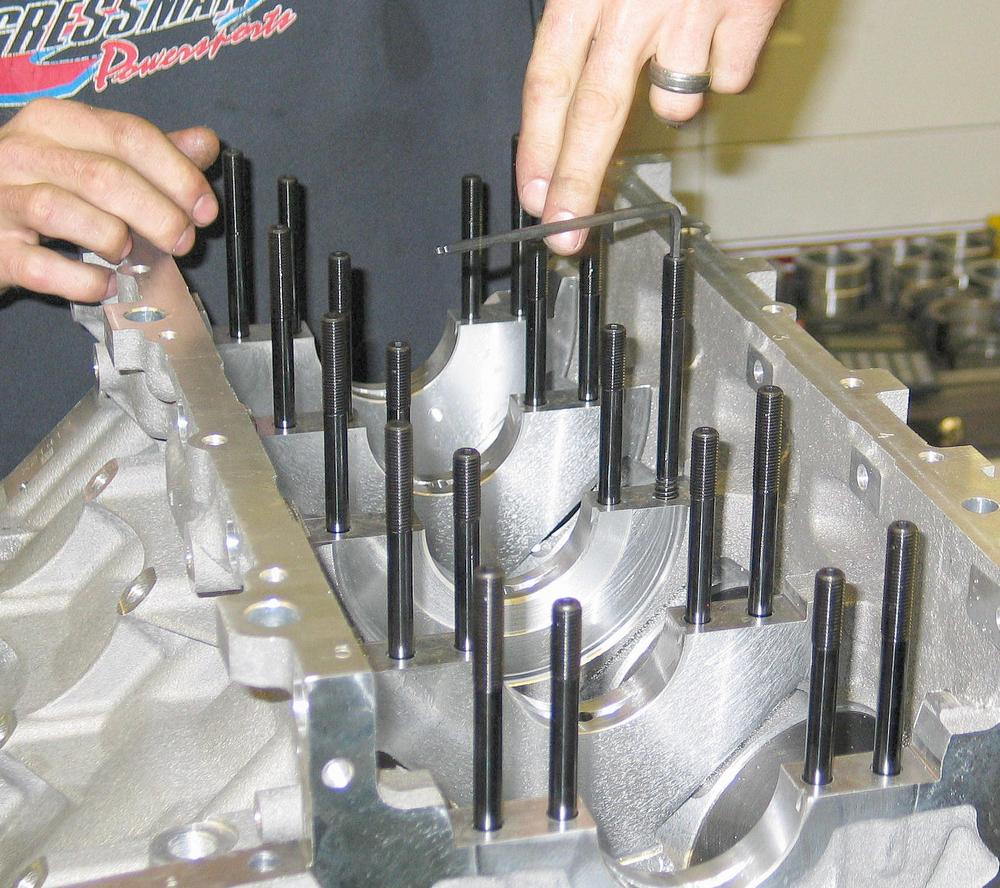
Agregar una forma de inducción forzada (turbocompresor o sobrealimentador) es un método popular y tentador para aumentar la potencia. Sin embargo, en lugar de atornillar a ciegas en un sistema de inducción forzada y tocar el pedal, primero considere los componentes internos del motor y su capacidad para soportar la potencia adicional.
Aquí discutiremos las áreas del motor de interés en términos de actualizaciones sugeridas. Los cambios/modificaciones / mejoras mencionados aquí no necesariamente generarán más energía, pero permitirán que el motor viva bajo el impulso anticipado. Si bien es genial considerar un refuerzo de potencia atornillado, necesitamos agregar un poco de seguro para darle al motor la oportunidad de sobrevivir.
Si bien agregar turbo o sobrealimentador a una melodía de, por ejemplo, 8 a 10 libras puede no requerir un replanteamiento extenso del bloque, el conjunto giratorio y alternativo, los niveles de refuerzo más altos (así como el uso extensivo de inyección de nitroso de alta potencia) pueden colocar suficientes tensiones adicionales que pueden causar estragos en un motor que de otra manera no estaría preparado. El viejo adagio del corredor «para terminar primero, debes terminar primero» se aplica aquí.
Tapas principales
Si planea crear presión adicional del cilindro y la tensión resultante en el extremo inferior, comience reforzando la disposición de la tapa principal que asegura el cigüeñal. Si planea bombear caballos de fuerza hasta el rango de 400 hp o más, puede agregar un aumento en la resistencia del extremo inferior cambiando de tapas principales de hierro fundido originales a tapas principales de palanquilla de acero.Se prefieren tapas de cuatro pernos
. Si el bloque se hizo originalmente con tapas de dos pernos, el bloque se puede taladrar y roscar para aceptar los dos pernos de tapa adicionales por ubicación principal.
Si el diseño del bloque lo permite, el uso de tapas principales «extendidas» de cuatro pernos es ideal. Esto contará con las dos ubicaciones de los pernos centrales verticalmente (90 grados a la línea central de la manivela), con las dos ubicaciones de los pernos exteriores colocadas en un ángulo que apunta hacia afuera hacia las áreas laterales principales de la banda. No todos los bloques de equipo original admiten una modificación a arreglos de cuatro o cuatro pernos extendidos. Si actualmente tiene un bloque de tapa principal de dos pernos, es posible que deba comprar un bloque que originalmente se hizo para aceptar tapas de cuatro pernos.
La holgura del rodamiento principal dependerá en parte del material del bloque. Los bloques de aluminio tienden a expandirse más que los bloques de hierro, lo que permite una holgura de rodamiento principal estática ligeramente más estrecha en un bloque de aluminio. La regla general es correr 0.001 pulgadas por pulgada de diámetro del árbol del cigüeñal. Para un motor impulsado, algunos constructores prefieren agregar aproximadamente 0.0005 pulgadas para generar una mayor cuña de aceite para soportar la manivela durante el funcionamiento.
De nuevo, en términos generales para la mayoría de los motores V-8, la holgura del rodamiento principal funcionará en el rango de 0,0025 pulgadas, pero naturalmente esto variará dependiendo del motor específico. Si el juego de cojinetes está demasiado suelto, es posible que el sistema de lubricación del motor no pueda satisfacer la demanda.
Cigüeñales
Cuanto mayor sea la potencia, mayores serán las tensiones experimentadas por el cigüeñal. Para cualquier construcción de alto rendimiento que se espera que escupa más de 450 CV, el cambio a un cigüeñal forjado de calidad es un movimiento inteligente.
Las manivelas de acero forjado son más resistentes que las manivelas fundidas y resistirán mejor las tensiones impuestas por las mayores presiones del cilindro. Dependiendo del nivel de potencia (y de impulso) y de cómo se utilizará/abusará del motor, una manivela fundida puede sobrevivir o no. Si está construyendo el motor desde cero y planea usar una cantidad saludable de impulso, ni siquiera considere una manivela fundida.
Nota: Si planea utilizar un sobrealimentador accionado por correa, el hocico de la manivela experimentará una mayor tensión, lo que es otra razón para usar una manivela forjada. Además, tenga en cuenta que un diseño de equipo original puede tener un hocico de manivela con llave o (en el caso del motor GM LS, por ejemplo) el hocico puede no tener llave, utilizando un amortiguador de ajuste a presión. Si planea hacer funcionar un sobrealimentador accionado por correa, asegúrese de que el hocico de la manivela se ajuste a esto.
Bielas
El esfuerzo adicional de cualquier sistema de inducción forzada (turbocompresor, sobrealimentador o incluso la inyección ocasional de óxido nitroso) coloca más tensión en las varillas. Cambiar de varillas de metal fundido o en polvo a varillas de acero forjado de calidad es una necesidad si planea funcionar con aproximadamente 450 hp o más.
¿Qué estilo es el mejor? En teoría, las barras de haz en H son más fuertes, pero en realidad una barra de haz en H puede ser más liviana mientras es tan fuerte como una barra de haz en I. Sin entrar en demasiados detalles, en muchos casos elegir entre vigas en I y vigas en H se reduce a la disponibilidad del fabricante o a la preferencia del fabricante del motor.
Otro estilo de viga es la viga X, que se ha utilizado en algunas aplicaciones diésel (para ahorrar peso), pero ahora también está disponible para varias aplicaciones de motores de gas automotrices. La viga X es una especie de mezcla de viga I y viga H, con ranuras que ahorran peso tanto en las caras como en los lados de la viga. Esto proporciona un ahorro de peso sustancial, al tiempo que aumenta la superficie de la viga, ofreciendo un peso más ligero y conservando la resistencia.
En resumen, si planea producir más de 450 HP, elegir una varilla forjada de calidad proporciona sustancialmente más seguro en comparación con una varilla de metal fundido o en polvo.
Igual de importante, o tal vez incluso más importante, es la calidad o la resistencia a la tracción de los pernos de varilla. Para cualquier construcción de alto rendimiento, y ciertamente una que contará con inducción forzada, independientemente del tipo de varilla que se use, siempre use un perno de varilla de posventa de alta resistencia, como los ofrecidos por ARP y otros. Nunca escatime en pernos de varilla.
La mayoría de las aplicaciones de uso duro (de alto rendimiento callejero y carreras) favorecerán la holgura de los cojinetes de varilla en el rango de 0,002 a 0,003 pulgadas. Las varillas de diario pequeño (2.00 pulgadas o más pequeñas) pueden salirse con una holgura ligeramente más estrecha, en el rango de 0.0020 a 0.0025 pulgadas. Las revistas más grandes (2.200 pulgadas y más grandes) pueden necesitar un poco más de espacio libre, en el 0.rango de 0029 a 0,0030 pulgadas.
Los motores de inducción forzada (turbos y sobrealimentadores) tienden a generar más calor en los rodamientos y pueden requerir algo en el rango de 0,0030 a 0,0034 pulgadas (lo que requiere usar un aceite de viscosidad más pesada). Sin entrar en los detalles de plataformas de motores específicas, todo lo que estamos haciendo aquí es proporcionar autorizaciones de estadio. Es mejor consultar con el fabricante de rodamientos las recomendaciones de inducción forzada.
Pistones
Dependiendo de la cantidad de impulso y la presión del cilindro resultante, los pistones de fundición original o hipereutécticos pueden no ser capaces de soportar el aumento de las temperaturas y la presión del cilindro. El uso de pistones forjados o de palanquilla de calidad es muy recomendable. Los pistones diseñados para inducción forzada suelen tener un área de cubierta de pistón más gruesa.
El espacio libre entre la falda y la pared del pistón para la mayoría de los motores V-8 generalmente estará en el rango de 0,0045 a 0,005 pulgadas y, dependiendo del pistón, puede ser de hasta 0,007 pulgadas. Con inducción forzada, manténgase en el lado máximo en términos de espacio libre de la falda.
En términos muy generales, para la inducción forzada, agregar aproximadamente 0,001 pulgadas de espacio libre por pulgada de diámetro interior es una práctica teóricamente aceptada. Pero esto siempre depende de la aleación específica y la densidad del material del pistón.
(Dado que los fabricantes de pistones de rendimiento/carreras utilizan fórmulas de aleación diferentes/patentadas, siempre siga el espacio libre de pared especificado por el fabricante de pistones.)
Los espacios libres de pared se listarán como un rango mínimo a máximo. Como una declaración muy, muy generalizada, los motores de bloques pequeños típicos usarán un espacio libre de pared de aproximadamente 0.004 pulgadas y los motores de bloques grandes típicos requerirán un espacio libre de aproximadamente 0.005 pulgadas (de nuevo, esta es una recomendación muy amplia).
Nota: Cuando se aumenta la holgura del faldón, puede haber una tendencia a experimentar una leve «bofetada» del pistón cuando el motor no se ha calentado a la temperatura de funcionamiento completa. Esto se puede resolver teniendo los faldones de pistón recubiertos de molibdeno, lo que proporciona una lubricidad adicional para proteger los faldones. La mayoría de los fabricantes de pistones de alto rendimiento ofrecen este revestimiento ya instalado.
Anillos de pistón
Dado que un sistema de inducción forzada (o el uso de inyección nitrosa) genera presión y calor adicionales en el cilindro, un espacio de anillo de especificación «estándar» puede ser demasiado apretado, ya que los pistones crecen en diámetro a medida que aumenta el calor (más con una presión de cilindro más alta).
Si el espacio es demasiado estrecho, los anillos pueden terminar uniéndose, lo que puede colocar una tensión indebida en la corona del pistón, lo que posiblemente resulte en una falla del pistón. Una regla general es aumentar ligeramente el espacio del anillo superior a una melodía de aproximadamente 0,006 pulgadas por pulgada de diámetro interior.
Por ejemplo, si el diámetro interior es de 4,125 pulgadas, es posible que el espacio del anillo superior deba estar en el rango de 0,025 pulgadas (o posiblemente mayor). Consulte siempre la recomendación del fabricante de pistones para aplicaciones de inducción forzada. El alto impulso requiere huecos de extremo de anillo «más sueltos».
Además, si el motor va a ser ayudado por inducción forzada y/o el uso de inyección de nitrógeno (en el rango de impulso de más de 100 caballos de fuerza o más), considere el uso de anillos superiores más fuertes, como anillos de acero nitrurados o con un revestimiento endurecido. Una vez más, consulte las recomendaciones del fabricante de pistones, ya que las especificaciones diferirán entre las aplicaciones aspiradas naturalmente y las impulsadas.
Orificios del cilindro
El uso de inducción forzada genera presión adicional del cilindro cuando está bajo impulso. Se debe tener en cuenta el grosor de la pared del cilindro para evitar la distorsión excesiva del orificio del cilindro (que afectará el contacto y el sellado del anillo), así como el posible agrietamiento de la pared del cilindro.
Los espesores de pared variarán no solo entre marcas y modelos de motores, sino también entre bloques de la misma familia. Sin profundizar en bloques específicos de año / marca / modelo, una regla general es que el grosor de la pared no debe ser inferior a aproximadamente 0.200 pulgadas. Durante su construcción, el taller de motores puede verificar esto fácilmente con un comprobador sónico portátil que mide el grosor del material.
Mi punto es verificar siempre el grosor de la pared del cilindro, especialmente si el bloque ha sido o será sobre-perforado.
Válvulas
Las válvulas de escape en un motor impulsado, particularmente con turbocompresor, están expuestas a mayores niveles de calor. Las opciones más populares en términos de materiales de válvula para aplicaciones de inducción forzada son un acero inoxidable de alto grado (comúnmente conocido como EV8) o Inconel, que resistirán temperaturas de válvula más altas.
Si no está familiarizado con Inconel, los beneficios básicos, a diferencia del acero inoxidable, incluyen un peso más ligero, una alta resistencia y una mayor resistencia a la dinámica térmica.
Las válvulas Inconel ofrecen una resistencia térmica extremadamente alta y están diseñadas para aplicaciones de alta temperatura, como las que se encuentran en aplicaciones turboalimentadas, sobrealimentadas y nitrosas.
Árbol de levas
Para optimizar el uso de la inducción forzada, lo ideal es que el motor prefiera un ángulo de separación de lóbulos (LSA) en el rango moderado-amplio, probablemente alrededor de 112 a 114 grados. En general, también se requieren resortes de válvula más pesados, dependiendo de la cantidad de impulso que se esté creando.
El escape se abre contra presión, por lo que esto no es una gran preocupación, pero con respecto al lado de admisión, es probable que necesite resortes de mayor velocidad. Consulte con el fabricante del árbol de levas para obtener su recomendación con respecto a las presiones de resorte.
Bujías
Como regla general, se recomienda ejecutar un rango de calor más frío que el stock con un sistema de inducción forzada. Si va a agregar un sistema de turbo o sobrealimentador, preste atención a las especificaciones de las bujías que se proporcionan en las instrucciones del kit.
Mejoras para Tener en cuenta la durabilidad
· Pistones (cambiar a aluminio forjado en lugar de hipereutéctico)
· Compresión más baja (cuando sea necesario) para acomodar una cantidad adicional de impulso
· Recubrimientos especiales (barrera térmica y antifricción)
· Bielas (cambiar a forjado en lugar de hierro fundido o metal fundido en polvo)
· Pernos de biela (cambiar a pernos de posventa de mayor resistencia a la tracción siempre es una buena idea)
· Cigüeñal (cambiar a forjado en lugar de fundido)
· Hocico de manivela de doble llave
· Amortiguador de manivela de acero/alto rendimiento
· Conversión a un amortiguador/polea con llave en una manivela de polea a presión LS
· Juntas de culata (cambiar a MLS en lugar de compuesto)
· Pernos de culata (en lugar de pernos)
· Tapas principales (acero de palanquilla en lugar de hierro fundido o metal en polvo)
· Pernos o pernos de la tapa principal (con mayor resistencia a la tracción)
· Faja de la tapa principal (dependiendo del motor)
· Válvulas (actualización potencial a válvulas inoxidables de mayor calidad y/o Inconel para válvulas de escape)
· Resortes de válvula de mayor velocidad/más duraderos
· Brazos basculantes (rodillos completos del mercado de accesorios más duraderos)
· Sistema de enfriamiento (asegúrese de que el sistema de enfriamiento existente esté limpio y funcione correctamente; y la posible necesidad de una bomba de agua y un radiador más eficientes, especialmente si se usa un intercooler)
Mejoras de revestimiento especiales
Mientras que algunos (principalmente constructores que no son motores) pueden burlarse de la utilidad del motor especial recubrimientos, hay ventajas distintivas que ofrecen varios recubrimientos para mejorar la durabilidad o el rendimiento, o ambos.
Mientras que una amplia gama de recubrimientos especializados están disponibles para adaptarse a una variedad de tareas, con respecto a los recubrimientos que se adaptan a configuraciones de inducción forzada, aquí nos centramos en los siguientes recubrimientos:
· Revestimiento de barrera térmica para cúpulas de pistón
· Revestimiento de barrera térmica para cámaras de combustión
· Revestimientos Moly (antifricción) para faldones y cojinetes de pistón
· Revestimientos de barrera térmica para caras de válvulas de escape y puertos de escape
· Revestimientos de barrera térmica para colectores de escape
una fórmula cerámica) proporciona lo que el término implica: una barrera térmica. Cuando se aplica a cúpulas de pistón, esto no solo ayuda a proteger el pistón del calor excesivo (generado a través de inducción forzada, especialmente en configuraciones de turbo), sino que este recubrimiento también ayuda a mejorar la potencia.
Más específicamente, mejora la eficiencia de la combustión, ya que el calor que de otro modo se empaparía en el pistón y la cámara de combustión ahora está mejor contenido y ayuda a la combustión más eficiente de la mezcla de combustible/aire.
Lo mismo se aplica al revestimiento de barrera térmica aplicado a las caras de las válvulas de escape y al interior de los orificios de escape de la culata. En lugar de perder calor (a través del remojo), el calor de combustión está «contenido» y se escurre en lugar de quedarse y sumergirse en los pistones, válvulas y cabezales. No solo es un revestimiento protector contra el calor, sino que debido a la eficiencia térmica, también puede (dependiendo de otros factores) proporcionar un ligero aumento de potencia.
Los recubrimientos antifricción (típicamente una fórmula a base de molibdeno) se pueden aplicar a una variedad de superficies, más específicamente a cojinetes de levas, varillas y principales y faldones de pistón. Si bien esto no proporcionará energía adicional, es una película protectora que ayuda a reducir las pérdidas por fricción y prolonga la vida útil de los componentes, principalmente durante arranques en frío y en entornos de alta temperatura/alto estrés (cuando realmente lo está martillando).
Por cierto, los recubrimientos especiales también están disponibles para componentes de sobrealimentadores y turbocompresores, que pueden proporcionar una mayor eficiencia y una mayor durabilidad. Si está interesado en mejorar estas unidades, póngase en contacto con el fabricante de inducción forzada y con los especialistas en recubrimientos. Pueden aconsejarle sobre disponibilidad y beneficios, y qué recubrimientos (si los hay) tienen más sentido para su aplicación. Ejemplos de servicios de recubrimiento incluyen recubrimientos Swain Tech, Polydyn y Calico.